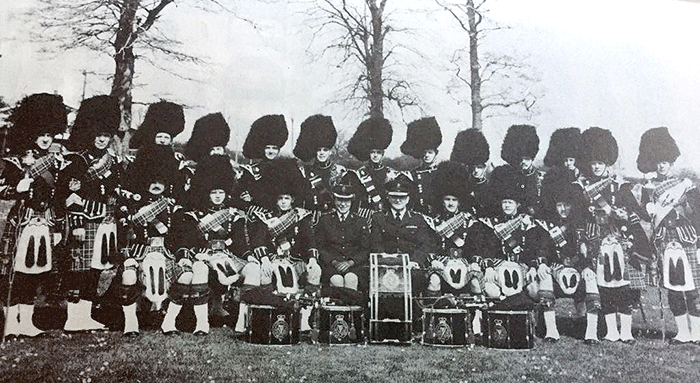
Alan Cardwell has kindly forwarded the above picture of the Royal Ulster Constabulary Pipe Band in 1977 featuring his father, the late Denver. The band is pictured with its first Chairman, Chief Constable Sir John Hermon. Alan tells me the band’s first practice of that year took place on February 9th.
If anyone has any more on the founding of the band, now known as the Police Service of Northern Ireland Pipes & Drums, or can identify the personnel pictured, we’d be very grateful for any information to the usual email.
Sound advice…..A week or so ago we featured the Singer Pipe Band of old. The company magazine ran regular articles on the band and in this short piece it enlightened the Clydebank sewing machine fraternity of the complexities of reed making:
‘The making of reeds is much more of an art than it is a science. With rare exceptions, the bulk of reed makers arrived at their end product via a tortuous path of trial and error and the same might be said of the pipe makers so far as the chanter is concerned. Whether a standard specified article will ever materialise remains to be seen and whether it would be a good thing or not is open to discussion.
‘Looking at the foregoing state of affairs, is it to be wondered at that the poor piper is bewildered and perplexed when beset by so many variables; surely no other instrumentalist is so sorely tried in this respect ?
‘Fortunately or unfortunately for the reedmaker, the bulk of the grumbling settles around his product and pipers spend fortunes and endless time in search of a consistent article which will give satisfactory results for a reasonable period of time.
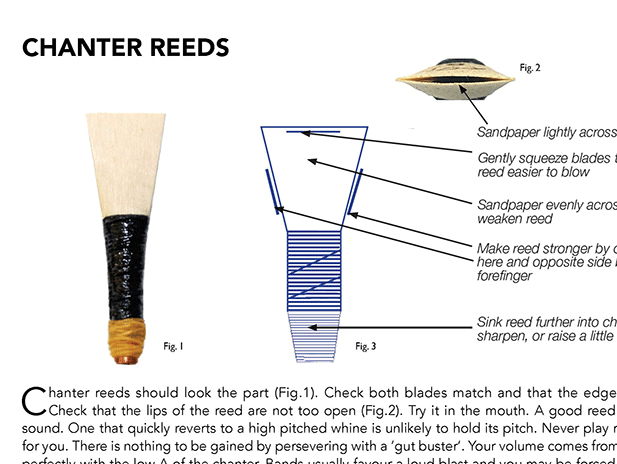
‘A novice going to purchase a reed on his own should never fail to take his chanter with him. Only in this way can the best results be hoped for. Many pipers seem to be under the impression that a reed should be perfect for strength and pitch, etc., from the first blow, and nothing could be more fallacious. Good reeds are built to stand up to a certain amount of heat and moisture and as a result should rise to their best under these conditions.
‘Playing tends to sharpen them, therefore a good reed should be slightly flat to begin with and require about ten to fifteen minutes playing to bring it to its best and it will only be good so long as it retains these qualities. It definitely is a mistake to buy a reed which seems to be ‘dead-on’ from the first blow, as the odds are so much against it standing up to a fair amount of playing.
‘Now then pipers, try blowing the reeds in, do not strangle them at birth and then expect to get good results; give the reed a chance and it will speak for itself.’ As I say, sound advice.
North east piping adjudicator Norman Matheson has featured in the local press, but this time it is not Norman’s piping connection that has attracted attention but a new book he has written and illustrated on the king of fish, the salmon.
The Press & Journal story reads: ‘Norman Matheson, 87, has been casting his line along the expanse [of the River Dee] for the better part of seven decades – and recently documented his passion for salmon in a book about the treacherous travels the fish undertake in their lifetime….
‘Prince Charles wrote the foreword for ‘A Speyside Odyssey’, praising Mr Matheson’s ‘unrivalled knowledge and infectious passion for the fascinating story of Atlantic salmon’ along with his ‘splendid watercolour illustrations’.
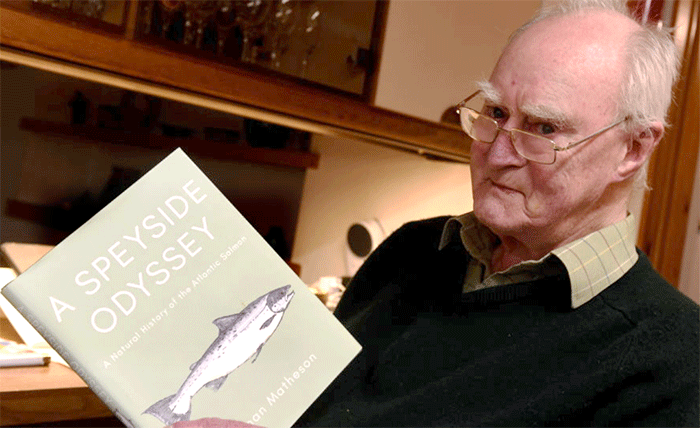
‘Mr Matheson, who worked as a surgeon at Aberdeen Royal Infirmary and still lives near the city, was brought up in Glenlivet and Tomintoul and fell in love with salmon fishing on the Spey as a boy.
‘The book took Mr Matheson almost three years to write, and he also delicately painted more than 40 watercolour illustrations of sea creatures, birds, wildlife, natural flowers and, of course, the Atlantic Salmon to illustrate it.’
Norman is no stranger to illustrations or royalty. He did the drawings for my ‘Silver Chanter’ book and a few years ago received an award from Prince Charles to mark 45 years of continuous service a a piping judge at Ballater Games.
Friends of the late Tommy Graham, Liverpool, will be pleased to know he got a real piper’s send off. His son Andy: ‘The funeral was yesterday, his coffin draped in a Graham plaid, his war medals and flowers. Piper Richie Wilson piped the cortege from the house to set it on its way, and it was met by a massed band of pipers and drummers from the area at the cemetery playing the Green Hills.
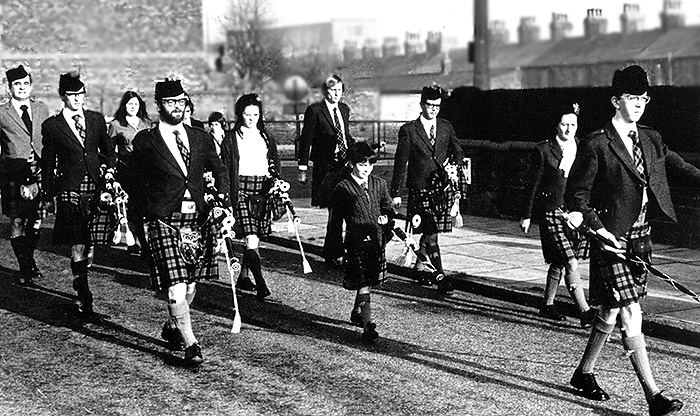
‘I played the ground of Catherine’s lament into the chapel and Lament for the Old Sword leaving. There was a small private ceremony inside with pipers and drummers waiting patiently outside. Richie played Mist Covered Mountains and Flowers of the Forest at the graveside in Allerton Cemetery.
‘It was followed by a small family gathering when the youngest member of the family, 12 week old Ben, put in an appearance and a toast was
given by Ian Graham.’
Tomorrow (Jan 25th) sees the big piping concert at Celtic Connections featuring Boghall & Bathgate Pipe Band. The blurb: ‘One of Celtic Connections’ longest-running fixtures, the annual Piping Concert for 2020 features one of the most illustrious ensembles in the field, the Peoples Ford Boghall & Bathgate Caledonia Pipe Band.
‘Founded in 1972, it’s been helmed [sic] since 2016 by Pipe Major Ross Harvey, together with Leading Drummer Gordon Brown, who’s held the role since 1991, having first joined the Novice Junior Band in 1976. Such continuity of membership, together with a focus on encouraging young players – who are taught by their Grade 1 seniors – has been integral to Boghall and Bathgate’s distinguished competitive record.’ More info.
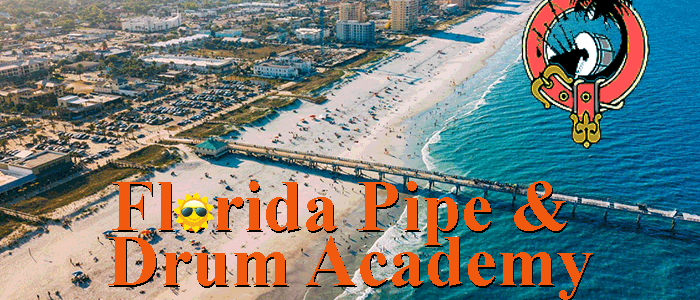
Reed making and purchasing is as described to me when I had a shot at it, is a lottery. Over the decades and years, I purchased quite a few makes and some proved to be nothing short of terrible. Occasionally a good one was discovered and that provided satisfaction. However, to be said, pipers live and love to ruin good reeds and I am no exception. Some years ago when I commenced hacking cane to bits in the quest to make reeds, I had a visit from 16 year old chap who played the oboe and he was considered good at his chosen instrument. He was curious as to how I made pipe chanter reeds. I demonstrated my efforts, thinking that it was a crude process. It involved preparing the cane from the tube, cutting the tube to length, splitting the tubes to slips, gouging out the pith, shaping the v profile, removing the hard bark and then shaping and thicknessing the blades. Then to cut the copper strip to then fashion a staple. Tie the lot together and then pitch the reed by cutting the tip. Luckily I got a reed to work OK. It was a relief. The chap seemed impressed and asked if I would like to see an oboe reed being made. I was enthusiastic about this.
He needed a door knob and a glass of water to carry out his demo. I obliged and he took from his pocket a couple of pieces of pre-gouged cane, an oboe staple and a length of thread. He had a shaper for the profile of the reed and of course a reed knife and a knife for trimming the profile. He had a mandrel onto which he put the staple. The cane was put into the glass of water and left for about 3 minutes. By the use of a bit of his thread, he married the blades together. He tied one end of a longish piece of thread to my door knob and then with some practiced skill bound the blades onto the staple. He had the advantage of the pre-gouged cane and ready made staple of course. However his demonstration took about 8 to 10 minutes, or fractionally longer. He did a bit of scraping with his reed knife, whipped out his oboe and played a tune!
I was gobsmacked and stated that I doubted that any 16 year old piper could do what he had done in regards to pipe chanter reeds. I suppose I will be corrected in my continuing doubt.
The young chap told me that what he had done was part of the instruction he got from his oboe teacher. I don’t know what goes on at teaching establishments re pipe chanter reed instruction re scraping, but this brief experience left me wondering.
It is now commonplace for newly purchased pipe chanters to be gouged and plastered with tape etc. Whether it is poorly made reeds and or poorly designed pipe chanters, or both is of interest. Of course it seems to be now a desire to gouge pitch holes and it will be required at times maybe because we cannot make good enough reeds and sticky tape is our solution. Musianship?
Duncan – I agree with your comments in your last paragraph – too many shortcuts and not enough patience to master this skill.
I believe it was the late PM Sandy Hain who made reeds in the Cleveland Ohio area for years. He told me that when you start to make reeds that you can figure to toss the first 1000 until you hit upon your sound. I have always felt that the problem with reeds is that the maker, no matter how much he makes all things equal, ie blade shaping, gouging and the staple size, doesn’t know what he has got until the blades are bound and the reed finally tested in a chanter. Why all the difference in sound from reed to reed, it has to be the variances in the cane material itself. Just some observation on my part.